Shelly Wave Pro Shutter US LR
-20240621-121613.png?inst-v=ebf6479b-b8d8-4c4a-93b6-13a430c63b58)
Device identification
Device: Shelly Wave Pro Shutter (US)
US Part number/Ordering Code: QUSH-0A1P10US
Z-Wave Product type ID: 0x0003
Z-Wave Product ID: 0x0085
Z-Wave Manufacturer: Shelly Europe
Z-Wave Manufacturer ID: 0x0460
This device supports both Z-Wave® (mesh) and Z-Wave® Long Range (star) network topologies. During the device inclusion process, you must select one type of network topology.
Bellow sections marked with * are valid only for Z-Wave® mesh network inclusion and are not applicable for Z-Wave® Long Range star network inclusion.
Terminology
Short description
The Device is a DIN rail mountable and enables remote control of motorized blinds, roller shutters, venetian blinds, awnings, etc. It measures power consumption of the connected device. It is recommended to use only motors with electronic or mechanical limit switches. The motor limit switches must be set correctly before connecting the Device to the motor.
Basic Functions
SmartStart
Assocciations
Working as Z-Wave repeater
Controls position of blinds, rollers, shades, venetian blinds, etc.
Controls tilt position of the slats of venetian blinds
Measuring Power consumption (W) and Energy consumption (kWh) of all connected loads.
OTA - Over-The-Air firmware update
Main applications
Residential
MDU (Multi Dwelling Units - apartments, condominiums, hotels, etc.)
Light commercial (small office buildings, small retail/restaurant/gas station, etc.)
Industrial (factories, power plants, water processing, refineries, etc.)
Government/municipal
University college
Farming
Integrations
Shelly Wave devices are developed on the world's leading technology for smart homes – Z-Wave.
This means Shelly Wave works with all certified gateways supporting Z-Wave communication protocol.
To make sure the functions of Shelly Wave products are supported on your gateway, we are regularly executing compatibility tests of our devices with different Z-Wave gateways.
Simplified internal schematics
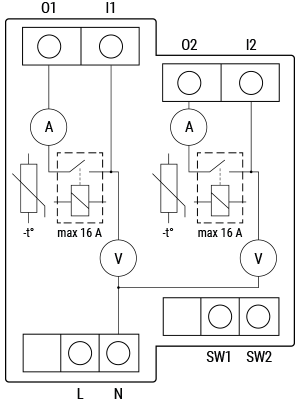
Device electrical interfaces
Inputs
2 switch/push-button inputs on screw terminal
2 relay inputs on screw terminal
2 power supply inputs on screw terminals: N , L
Outputs
2 relay outputs with power measurement on screw terminal
Connectivity
Z-Wave - Unsecure, S0 Security, S2 Unauthenticated Security, S2 Authenticated Security
Safety features
Overheat Protection
Supported load types
Inductive with RC Snubber (120 V AC electric motors)
User interface
S button and operating modes
Settings mode:
Is required to start the desired procedure, for example: adding (inclusion (*not available for Long Range devices)), removing (exclusion), factory reset, etc. It has a limited operating time. After completing the procedure in Setting mode, the Device automatically switches to Normal mode.
Entering Setting mode:
Press and hold the S button on the Device until the LED turns solid blue.
An additional quick press on the S button changes the menu in an infinite loop.
The Menu LED status has a timeout of 10s before entering again into Normal mode.
S button’s functions
Manually adding the Device to a Z-Wave network (*not available for Long Range inclusion)
Manually removing the Device from a Z-Wave network
Factory Reset the Device
Calibration
LED Signalisation
LED blinking modes
Specifications
Power supply | 120 V AC, 50/60 Hz | |
Power consumption | < 0.3 W | |
Power measurement [W] | Yes | |
Max. switching voltage AC | 120 V | |
Max. switching current AC | 12.5 A per channel | |
Overheating protection | Yes | |
Overcurrent protection | Yes | |
Overvoltage protection | Yes | |
Long range network | Distance (depends on local condition) | Up to 80 m indoors (262 ft.) or up to 1000 m outdoors (3281 ft.) |
Z-Wave® repeater | No | |
Z-Wave® frequency bands | 912.0 MHz | |
Mesh network | Distance (depends on local condition) | Up to 40 m indoors (131 ft.) |
Z-Wave® repeater | Yes | |
Z-Wave® frequency bands | 908.4 MHz | |
CPU | Z-Wave® S800 | |
Size (H x W x D) | 94x19x69 ± 0.5 mm / 3.70x0.75x2.71 ± 0.02 in | |
Weight | 75 g / 2.65 oz. | |
Mounting | DIN rail | |
Screw terminals max. torque | 0.4 Nm / 3.54 lbin | |
Conductor cross section | 0.5 to 2.5 mm² / 20 to 14 AWG (green connector) | |
Conductor stripped length | 6 to 7 mm / 0.24 to 0.28 in (green connector) | |
Shell material | Plastic | |
Color | Black | |
Ambient temperature | -20°C to 40°C / -5°F to 105°F | |
Humidity | 30% to 70% RH | |
Max. altitude | 2000 m / 6562 ft. |
Basic wiring diagram
![]() Fig.2 | ![]() Fig.1 |
---|
Legend
Device terminals:
N: Neutral terminal
L: Live terminal(s) (120 V AC, 50/60 Hz)
SW1: Input terminal for switch/push-button UP (open)
SW2: Input terminal for switch/push-button DOWN (close)
I1: Input terminal for motor UP (open)
I2: Input terminal for motor DOWN (close)
O1: Output terminal for motor UP (open)
O2: Output terminal for motor DOWN (close)
Wires:N: Neutral wire
L: Live wire (120 V AC, 50/60 Hz)
Button:S: S button
If you want to use the Device with a push-button, refer to the Fig. 1. For a switch, refer to the Fig. 2.
Connect L, I1 and I2 terminals to the Live wire and the N terminal to the Neutral wire. Connect the common motor terminal/wire to the Neutral wire. Connect motor direction terminals/wires to the O1 and O2 terminals.* Connect the first switch/push-button to the SW1 terminal and the Live wire. Connect the second switch/push-button to the SW2 terminal and the Live wire.
In case the inputs are configured as push-buttons:
Pressing the push-button when the blind is static, moves the blind in the corresponding direction until the endpoint is reached.
Pressing the push-button for the same direction while the blind is moving, stops the blind.
Pressing the push-button for the opposite direction, while the blind is moving, reverses the blind movement until the endpoint is reached.
In case the inputs are configured as switches:
Turning the switch on moves the blind in the corresponding direction until the endpoint is reached.
Turning the switch off stops the blind movement.
If both switches are turned on, the Device respects the last engaged switch. Turning off the last engaged switch stops the blind’s movement, even if the other switch is still on. To move the blind in the opposite direction, the other switch has to be turned off and on again.
Device can detect obstacles. If an obstacle is present, the blind movement will be stopped and, if configured so in the Device settings, reversed until the endpoint is reached. Obstacle detection can be enabled or disabled for only one of the directions or for both.
NOTE: This Device does not support the use of two separate ON/OFF switches. It is recommended to use a single double throw center OFF switch type.
*The Device outputs can be reconfigured to match the required rotation direction.
Operational Instructions
About Z-Wave®
Adding and removing the Device to a Z-Wave® network
Z-Wave® Security and Device Specific Key (DSK)
Z-Wave® Parameters
Z-Wave® Command Classes
Z-Wave® Notifications Command Class
Z-Wave® Associations
Z-Wave® Important disclaimer
Z-wave® wireless communication may not always be 100% reliable. This Device should not be used in situations in which life and/or valuables are solely dependent on its functioning. If the Device is not recognized by your gateway or appears incorrectly, you may need to change the Device type manually and ensure that your gateway supports Z-wave Plus® multi-channel devices and Z-wave® Long Range capability in case of Long Range devices.
Troubleshooting
For troubleshooting please visit our support portal: Support
Compatibility with gateways
Wave Pro Shutter | functions - reports | ||||||||
Gateway | Up | Down | SW Up | SW down | W | kWh | Slats | SW Slats | Notes |
Home Assistant |
|
|
|
|
|
|
|
| |
Fibaro HC 3 / Z-Wave engine 3 |
|
|
|
|
|
| |||
Homey | |||||||||
Homee Cube Gen 7 |
|
|
|
|
|
| ❌ | ❌ | *1 |
Homee Cube Gen 5 |
|
| P | P | ❌ | ❌ | ❌ | ❌ | *1, *2, *3 |
Smart Things | TBD | TBD | TBD | TBD | TBD | TBD | TBD | TBD | |
Vera Ezlo |
|
|
|
|
|
|
|
| |
Cozify |
|
|
|
|
|
|
|
| |
Notes | *1 The slats cannot be controlled through the UI and their position cannot be visualized due to the lack of control. |
Function | Meaning / tested |
---|---|
On/Off | if device respond to the app UI On/Off command |
SW On/Off | if device reports On/Off changes by SW input |
Dimming | if device respond to app UI dimming command |
SW Dimming | if device report dimming state change by SW input |
Watts | if Watts are reported (unsolicited) |
kWh | if kWh are reported (unsolicited) |
Up/Down | if device respond to the app UI Up/Down command |
SW Up/Down | if device reports Up/Down changes by SW input |
Slats | if the slats respond to the app UI command |
SW Slats | if the slats report the changes done by SW |
D control | detached mode if device reports scene commands single press, double press,… |
D Binary | detached mode if the device reports binary On/Off by SW input |
Sensor # | Is the sensor report visualized in the gateway, type of sensor in the notes. |
Legend | ||||
Symbol | State | |||
Working / Possible | ||||
❌ | Not Working / Not Possible | |||
P | Partially | |||
N/T | Not Tested | |||
TBD | To be done |
Gateway guides
You may find useful guides on gateways in the Z-Wave Shelly Knowledge base.
Disclaimers and Warnings
READ BEFORE USE
This document contains important technical and safety information about the Device, its safe use and installation.
Compliance
Disposal and Recycling
This refers to the waste of electrical and electronic equipment. It is applicable in the US and other countries to collect waste separately.
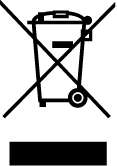
This symbol on the product or in the accompanying literature indicates that the product should not be disposed of in the daily waste. Shelly Wave Pro Shutter must be recycled to avoid possible damage to the environment or human health from uncontrolled waste disposal and to promote the reuse of materials and resources. It is your responsibility to dispose of the device separately from general household waste when it is already unusable.
FCC Notes
This Device complies with Part 15 of the FCC Rules.
Operation is subject to the following two conditions: (1) this device may not cause harmful interference, and (2) this device must accept any interference received, including interference that may cause undesired operation.
The manufacturer is not responsible for any radio or TV interference caused by unauthorized modification or change to this equipment. Such modifications or change could void the user’s authority to operate the equipment.
This equipment has been tested and found to comply with the limits for a Class B digital device, pursuant to part 15 of the FCC Rules. These limits are designed to provide reasonable protection against harmful interference in a residential installation. This equipment generates, uses and can radiate radio frequency energy and, if not installed and used in accordance with the instructions, may cause harmful interference to radio communications. However, there is no guarantee that interference will not occur in a particular installation. If this equipment does cause harmful interference to radio or television reception, which can be determined by turning the equipment off and on, the user is encouraged to try to correct the interference by one or more of the following measures:
Reorient or relocate the receiving antenna.
Increase the separation between the equipment and receiver.
Connect the equipment into an outlet on a circuit different from that to which the receiver is connected.
Consult the dealer or an experienced radio/TV technician for help.
RF exposure statement:
This equipment complies with FCC radiation exposure limits set forth for an uncontrolled environment. The device has been evaluated to meet general RF exposure requirement. The device can be used in portable exposure condition without restriction.
Printed User Guide
Shelly_Wave_Pro_Shutter_US_LR_V1_-print.pdf
Manufacturer
Shelly Europe Ltd.
Address: Shelly Europe ltd, 51 Cherni Vrah Blvd., building 3, floor 2 and 3, Lozenetz Region, Sofia 1407, Republic of Bulgaria
Tel.: +359 2 988 7435
E-mail: zwave-shelly@shelly.cloud
Support: https://support.shelly.cloud/
Changes in the contact data are published by the Manufacturer at the official website: https://www.shelly.com
Legal Notice
This User Guide is subject to change and improvement without notice. Shelly Wave reserves all rights to revise and update all documentation without any obligation to notify any individual or entity.